The purpose of sugar mold silicone:
Sugar Art Mold Silicone is mainly used in sugar art cakes, food silicone molds, sugar turning cakes, food appliance companies, food appliance design, sugar turning, baking, multi connection silicone cake baking plates, cake edge sugar turning accessories decoration cakes, sugar turning numbers and letters patches, sugar turning relief works, sugar turning flat patches, sugar turning cake models, biscuit candy molds, cake embossing printing silicone molds, lace sugar turning molds, frosting molds, The production of molds such as sugar art silicone printing embossing pads.

Sugar Art Mold Silicone Description:
Sugar mold silicone, also known as additive silicone, is a two component additive silicone. It consists of two parts: component A is silicone, and component B is silicone containing curing agent; Mix the two components in a 1:1 ratio.
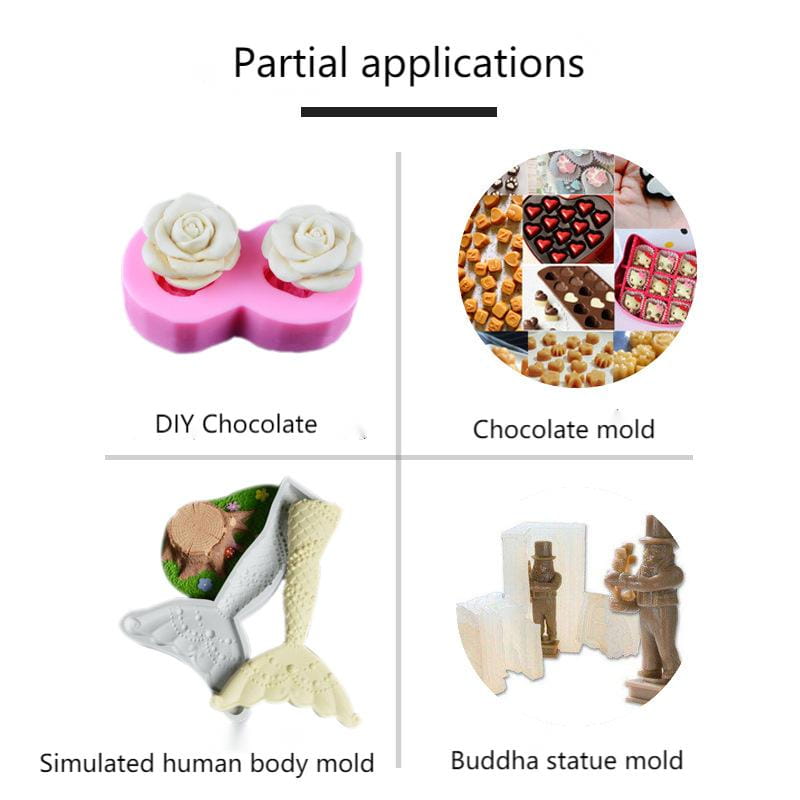
Features of Sugar Art Mold Silicone:
1. It has excellent high-temperature resistance, with temperatures ranging from 300 to 500 degrees.
2. Food grade, non-toxic and odorless, passing FDA food grade certification.
3. No shrinkage, high precision. It can solve products that cannot be made by film pressing machines, filling the gap in the production of large lead-tin alloy processes and fine patterned products. It is currently the most advanced HTV-2 high-temperature adhesive in China and the preferred material for lead-tin alloy handicrafts and precision mold manufacturing.
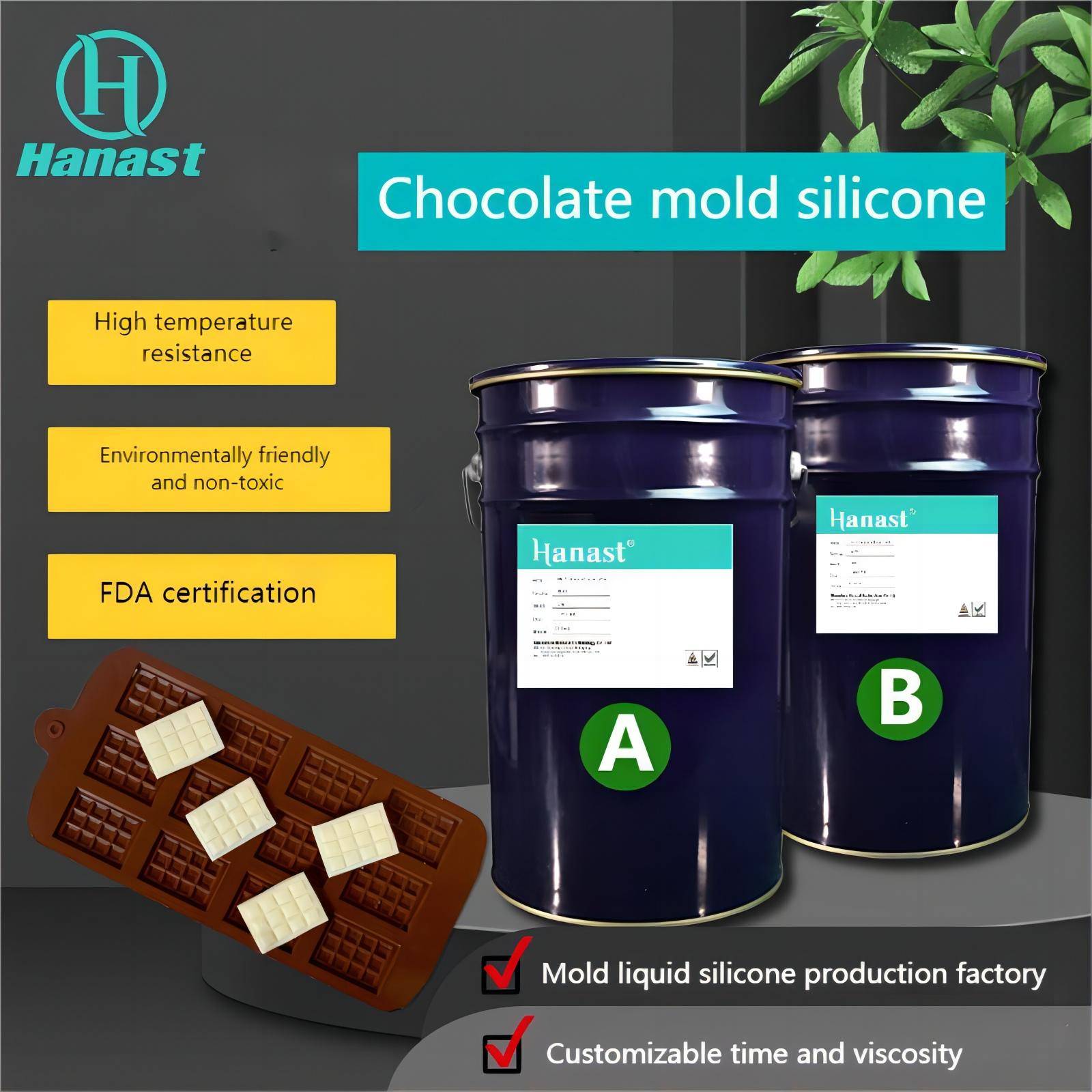
The production process of sugar cake silicone:
1. Preparation of tools and materials
Additive liquid mold silicone, one mold type (mother mold), one electronic scale, one stirring container, one stirring knife, and other tools and materials.
2. Model processing
Polish and polish the surface of the mold to be smooth, and then apply release agent. The release agent must be evenly applied (the release agent can be detergent, soapy water, Vaseline, liquid paraffin, etc.), and finally dry with a hair dryer or gauze. If making a split mold, choose to draw the mold line well.
PS: Uneven application of release agent can easily cause the mold seed to stick to the mold during demolding, damaging the mold seed and also damaging the mold.
3. Fixed mold type
Fix the mold with glue on the wooden board, and then process the mold according to different mold opening methods, including pouring mold, wrapping mold, and split mold opening methods.
If it is a pouring mold:
Injection mold or injection mold, suitable for relatively smooth or simple products, without mold lines, saving labor and time; The product or model to be copied should be enclosed with a rubber or glass board, and sealed around with glue to prevent the silicone from flowing out along the gaps when injecting silicone.
PS: Release agent should also be applied to the area where the rubber or glass board comes into contact with silicone.
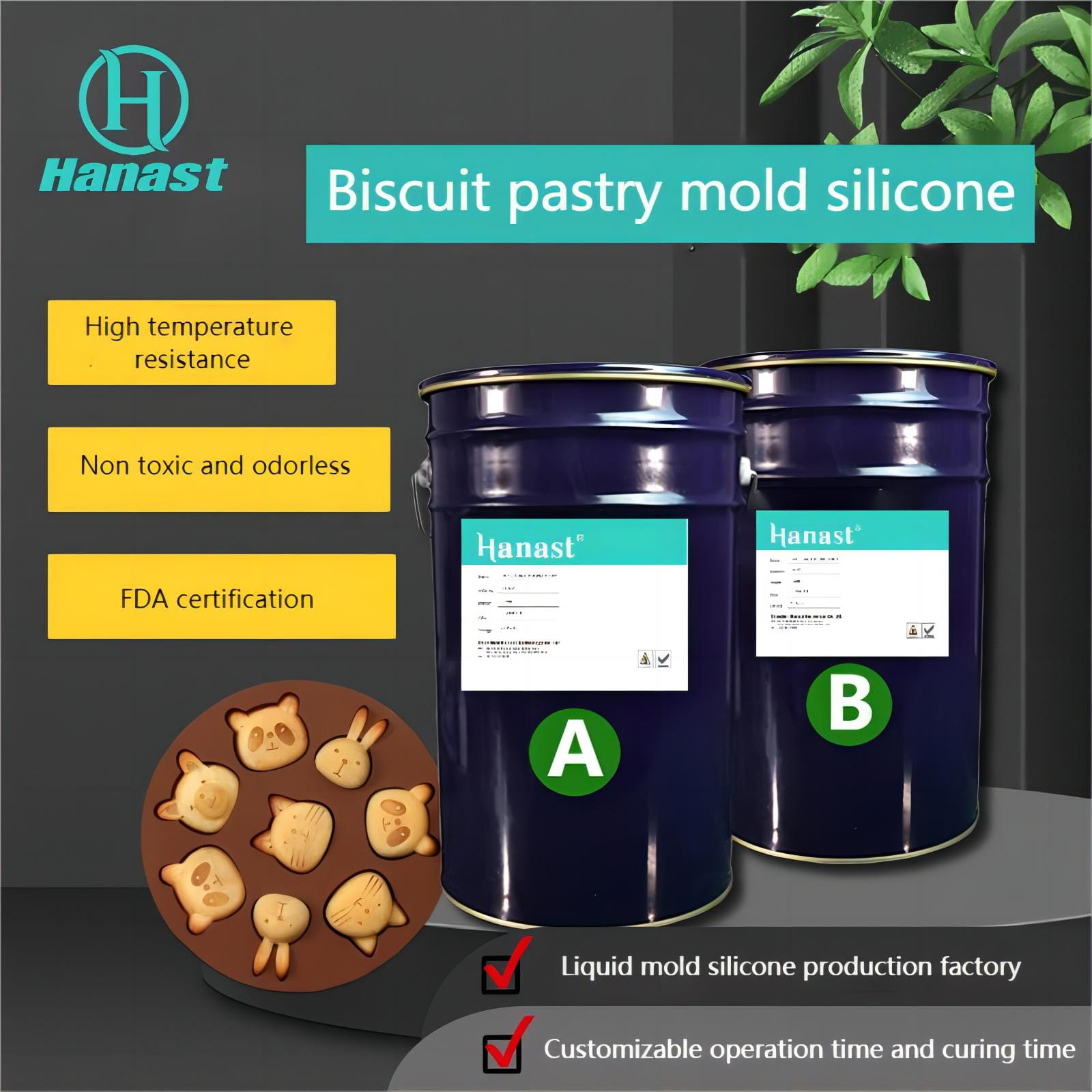
If it is a split mold:
Fill the part below the mold line with oil mud, grind it flat and smooth, and use a knife to cut off the oil mud around. The thickness between the oil mud and the mold seed should be 1cm-1.5cm.
4. Ratio of silicone two component
Mix the liquid mold silicone AB components in a 1:1 ratio and stir evenly.
5. Vacuum treatment
After mixing the silicone and curing agent evenly, proceed with the vacuuming and exhaust bubble process. The vacuuming time should not be too long, and under normal circumstances, it should not exceed ten minutes. If the vacuuming time is too long, the silicone will immediately solidify, causing cross-linking reactions, making it difficult to apply or pour the silicone one by one. This wastes the silicone, and the silicone can only be poured into the trash can and re taken for processing.
6. Mold glue operation process
Generally, painting or pouring operations are carried out, mainly divided into: pouring mold, wrapping mold, and slicing mold.
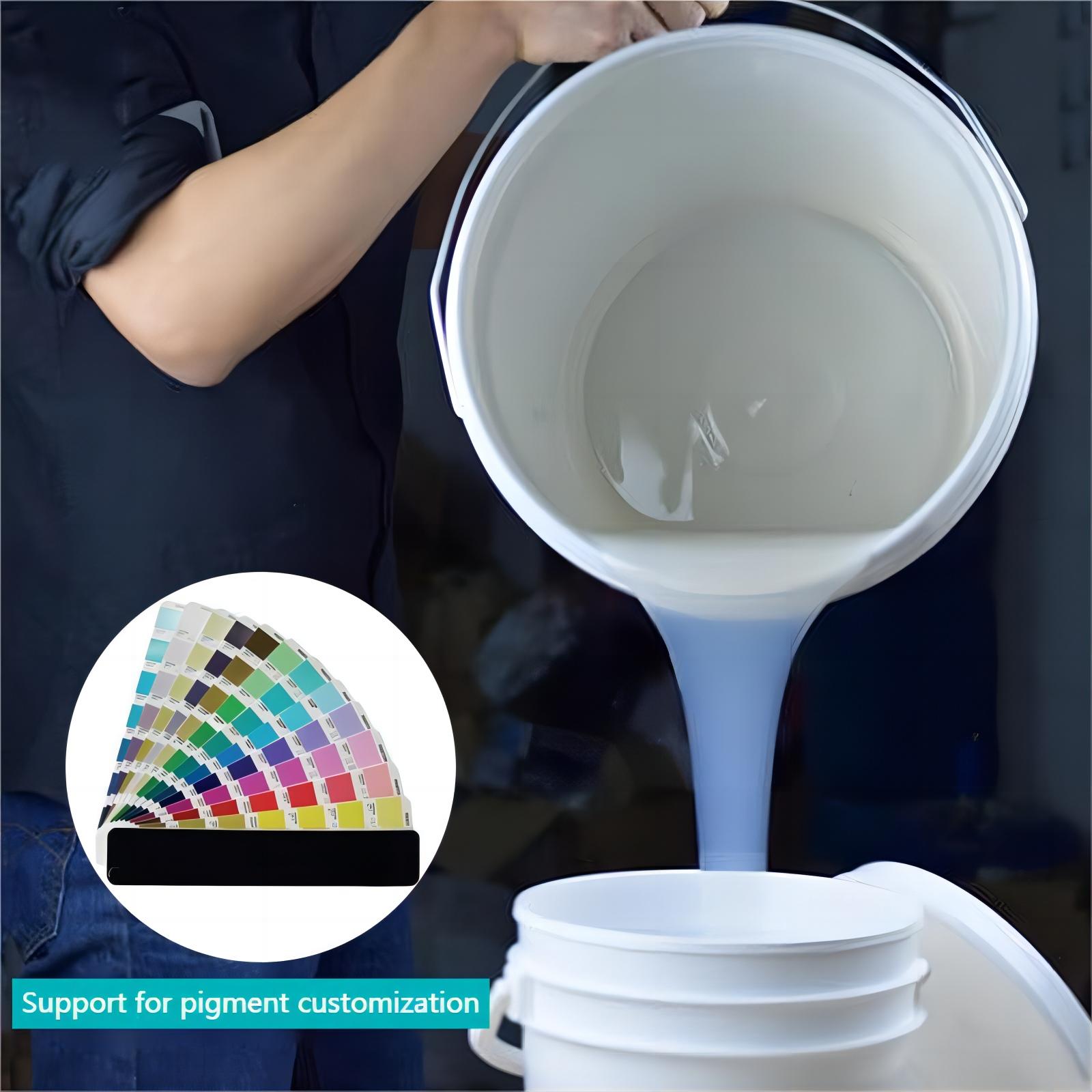
1) Operation method for pouring mold or pouring mold:
After fixing the mold according to the mold type, pour the vacuum filled silicone directly onto the product. After the silicone is dried and formed, take out the product, and the mold is formed (note: The injection mold usually uses soft silicone to make the mold, which is easier to demould and does not damage the products inside the silicone mold).
2) Operation method for wrapping or dividing molds:
Apply or pour the silicone that has been evacuated and drained of bubbles. Pour onto the product (note: products or models that need to be replicated before pouring silicone must be coated with release or isolation agents). Then apply the silicone onto the product evenly, and after 30 minutes, stick a layer of gauze and weft cloth to increase the strength and tension of the silicone. Then apply another layer of silicone and stick a layer of gauze and fiber weft cloth, so that after two passes, it will be ready. Only by doing so can the service life and turnover times of the developed silicone mold be significantly improved, which can save costs and improve efficiency. If it is a large product, fiberglass cloth can also be pasted, but fiberglass cloth cannot be pasted on the first layer because it is relatively hard and the inside of the mold will not be smooth.
3) The production of external mold: The general method and materials used are to surround the mold with adhesive boards or wooden boards. One method is to fill the mold cabinet with gypsum, and the other method is to use resin coating. After applying a layer of resin, a layer of fiberglass cloth is pasted, and then coated and pasted again. Repeatedly applying two or three layers can complete the external mold of the mold.
COMPANY PROFILE
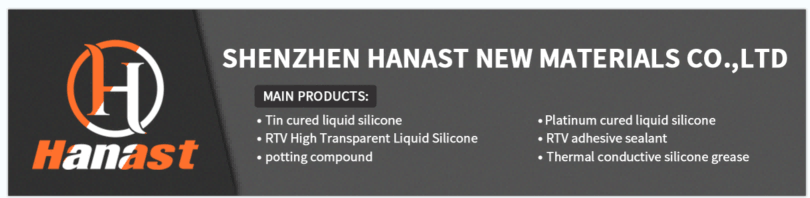
Shenzhen Hanast Technology Co, Ltd. was established on 2019. The factory is located in Sanming City, Fujian Province,
covering an area of 20,000 square meters.
Hanast is a silicone raw material company integrating R&D, production and sales, mainly engaged in conventional silicone
rubber,special silicone rubber, RTV adhesive sealant, two-component electronic potting adhesive, thermally conductive
silicone, thermally conductive silicone grease, lubricating silicone grease, damping silicone grease, platinum vulcanizing
agent and other silicone raw materials.
The products comply with ROHS standard, obtain SGS, Food Grade Certification, and the enterprise passed ISO9001. 2015
certification. Our products have obtained many national invention patents and utility model patents, and are widely used in
silicone kitchenware, high temperature wire and cable, industrial silicone rollers, medical industry, baby products, sporting
goods, adult products, new energy vehicles and other fields.
CERTIFICATIONS
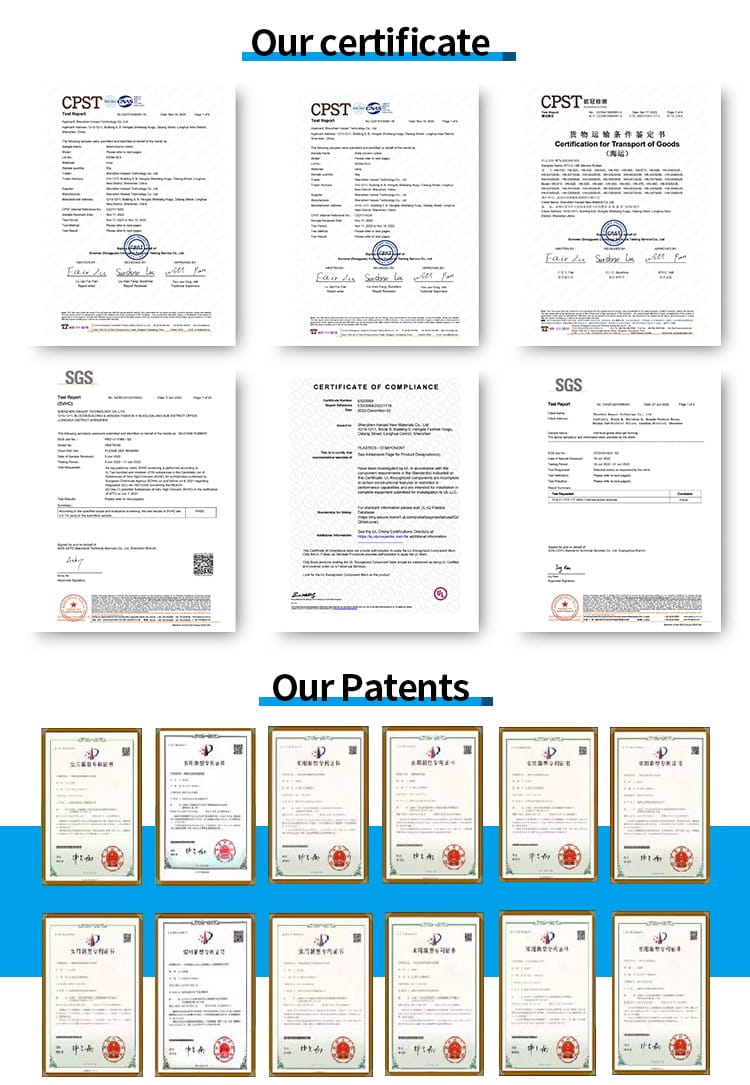
CUSTOMERS