potting glue is mainly used in industries such as automotive electronics, industrial filters, household appliances, and LED lamp casings. Polyurethane potting glue, organic silicon potting glue, and epoxy resin potting glue are poured into electronic components using equipment or manual methods, and cured into high-performance thermosetting polymer insulation materials at room temperature or heating conditions, thereby achieving the purpose of adhesion, sealing, and sealing. Let's talk about the types, functions, and how to choose the appropriate potting glue for HANAST.
The main function of potting is:
1. Strengthen the integrity of electronic devices and improve their resistance to external impacts and vibrations;
2. Improving the insulation between internal components and circuits is beneficial for device miniaturization and lightweight;
3. Avoid direct exposure of components and circuits, improve the waterproof, dust-proof, and moisture-proof performance of components;
4. Heat transfer and thermal conductivity;
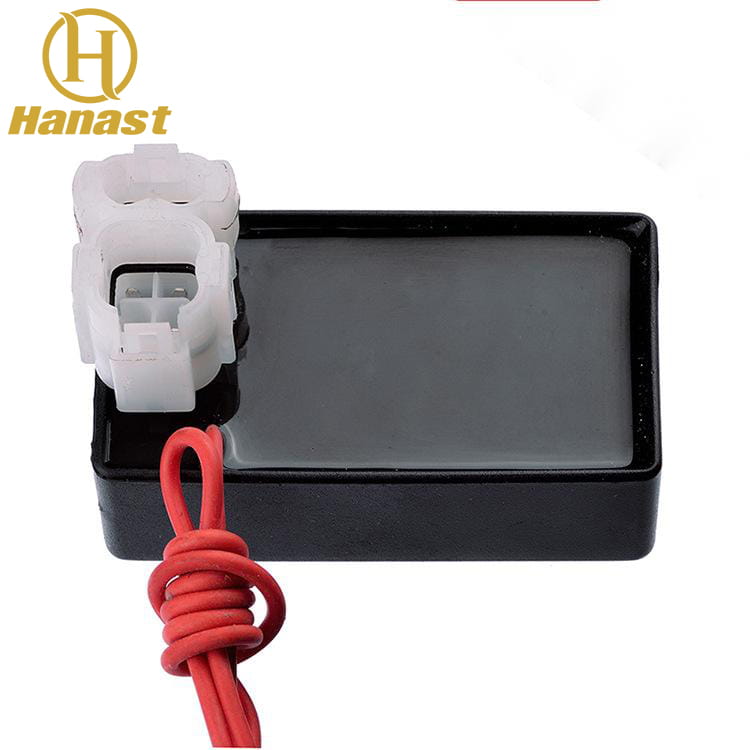
Advantages and disadvantages of three types of potting glue:
1. Epoxy resin potting glue
The epoxy resin sealing adhesive is mostly hard and almost as hard as stone after curing, making it difficult to remove. It has a good confidentiality function, but there are also a few soft parts. Ordinary ones have a temperature resistance of around 100 ℃, those cured by heating have a temperature resistance of around 150 ℃, and there are also those with a temperature resistance of over 300 ° C. It has characteristics such as fixation, insulation, waterproofing, oil resistance, dust prevention, theft prevention, corrosion resistance, aging resistance, and resistance to cold and hot impacts. Common types of epoxy sealant include flame retardant, thermally conductive, low viscosity, and high-temperature resistant.
Advantages: Good adhesion to hard materials, excellent high-temperature resistance and electrical insulation ability, simple operation, very stable before and after curing, excellent adhesion to various metal substrates and porous substrates.
Disadvantages: Weak resistance to cold and hot changes, easy to produce cracks after being subjected to cold and hot shocks, causing water vapor to seep into electronic components from the cracks, and poor moisture-proof ability. After solidification, the colloid has a high hardness and brittleness, which makes it easy to pull electronic components and cannot be opened after sealing, resulting in poor repair performance.
Scope of application: Epoxy resin sealing adhesive is easy to penetrates the gaps of products, suitable for sealing small and medium-sized electronic components at room temperature without special requirements for environmental mechanical properties, such as automotive and motorcycle igniters, LED drive power supplies, sensors, ring transformers, electrical containers, triggers, LED waterproof lights, and circuit boards for confidentiality, insulation, and moisture-proof (water) sealing.
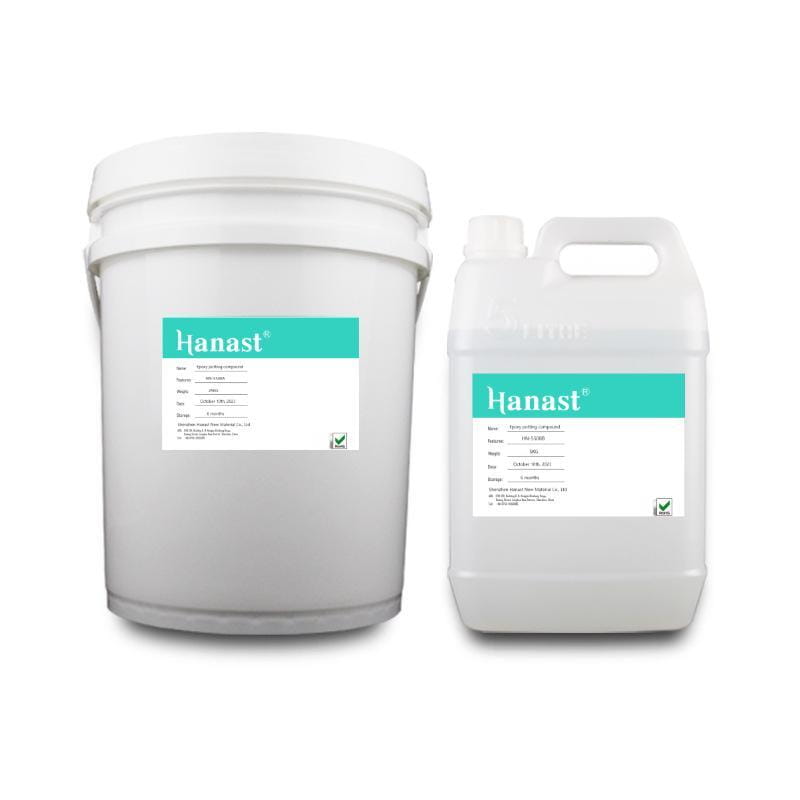
2. Organic potting compound
After curing, organic silicon electronic sealing adhesive is mostly soft and elastic, which can be repaired, abbreviated as soft adhesive, and has poor adhesion. Its color can generally be adjusted as needed, whether transparent, nontransparent, or colored. Two-component silicone sealant is the most common type, which includes two types: condensation type and additive type. Generally, condensed materials have poor adhesion to components and encapsulation cavities, and volatile low molecular substances are produced during the curing process, resulting in a significant shrinkage rate after curing; The addition molding (also known as silicon gel) has a very small shrinkage rate, and will not produce volatile low molecular substances during the curing process, which can be heated for rapid curing.
Advantages: strong aging resistance, good weather resistance, excellent impact resistance; It has excellent resistance to cold and hot changes and thermal conductivity, and can be used in a wide range of working temperatures. It can maintain elasticity within the temperature range of -60 ℃ to 200 ℃ without cracking and can be used for a long time at 250 ℃. The heating and curing type has higher temperature resistance, excellent electrical and insulation properties, and better insulation performance than epoxy resin, with a voltage resistance of over 10000V. After sealing, it effectively improves the insulation between internal components and circuits, and enhances the stability of electronic components; Has no corrosiveness to electronic components and does not produce any by-products during curing reactions; Has excellent repair ability, can quickly and conveniently remove sealed components for repair and replacement; Having excellent thermal conductivity and flame retardancy, effectively improving the heat dissipation capacity and safety factor of electronic components; Low viscosity, good fluidity, able to penetrate small voids and underneath components; It can be cured at room temperature or high temperature, with good self-foaming properties and more convenient use; The curing shrinkage rate is small, and it has excellent waterproof performance and seismic resistance.
Disadvantages: High price and poor adhesion.
Scope of application: Suitable for sealing various electronic components that work in harsh environments.
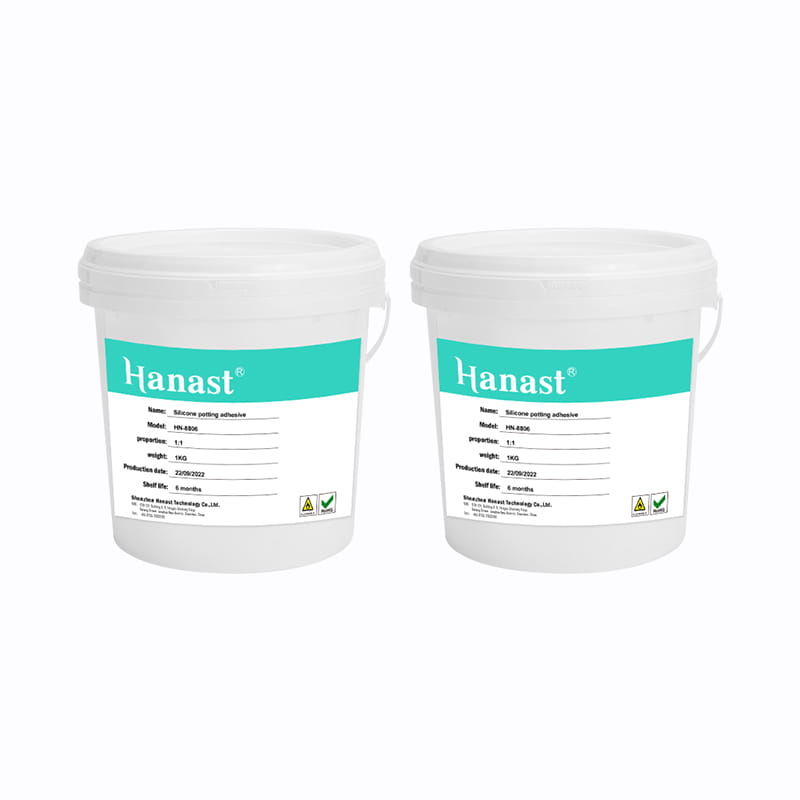
3. Polyurethane potting glue
Polyurethane sealing adhesive, also known as PU sealing adhesive, is mostly soft and elastic after curing, which can be repaired. It is abbreviated as soft adhesive, and its adhesive properties are between epoxy and silicone. It has average temperature resistance and generally does not exceed 100 ° C. After sealing, there are more bubbles, and the sealing conditions must be under vacuum. The adhesive properties are between epoxy and silicone.
Advantages: Good low-temperature resistance and the best shock-absorbing performance among the three. It has characteristics such as low hardness, moderate strength, good elasticity, water resistance, mold resistance, shock resistance, and transparency. It has excellent electrical insulation and flame retardancy and is non-corrosive to electrical components. It has good adhesion to metals such as steel, aluminum, copper, and tin, as well as materials such as rubber, plastic, and wood.
Disadvantages: poor high-temperature resistance, uneven surface and poor toughness of the gel after curing, weak anti-aging ability and UV resistance, and easy discoloration of the gel. Scope of application: Suitable for sealing indoor electrical components with low heat generation, it can prevent installed and debugged electronic components and circuits from being affected by vibration, corrosion, moisture, and dust. It is an ideal sealing material for moisture and corrosion prevention treatment of electronic and electrical components.
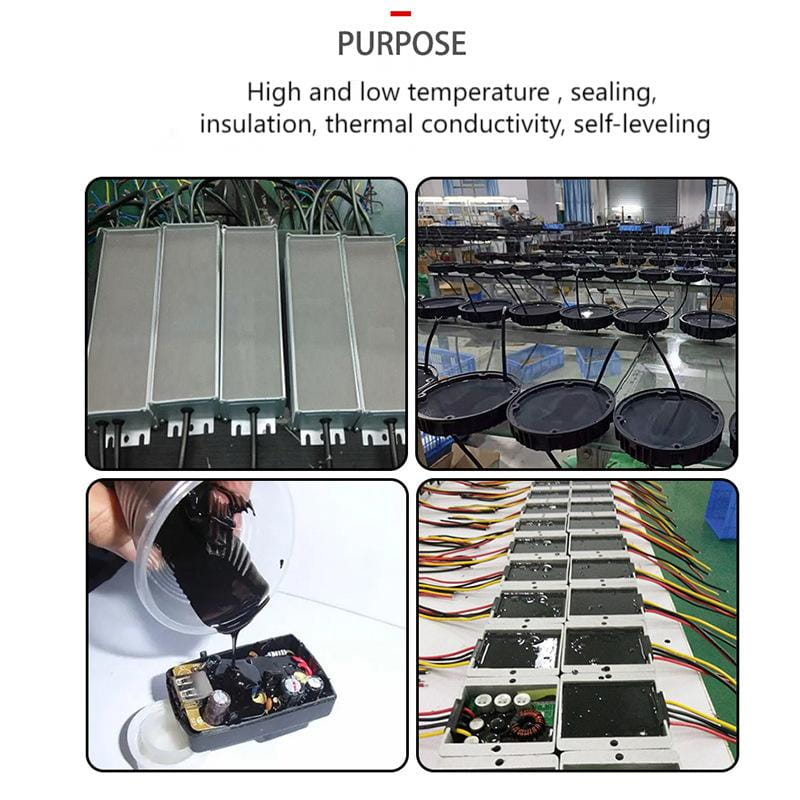